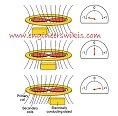
Introduction
Inductive encoders are a crucial component in many modern technologies, including robotics, automation, and mechatronics. They are used to measure the position, angle, or velocity of a rotating shaft or axle, providing vital feedback information for control systems. In this guide, we will delve into the world of inductive encoders, exploring their principles, types, applications, and benefits.
How Do Inductive Encoders Work?
Inductive encoders use the principle of electromagnetic induction to measure the position or angle of a rotating shaft. The basic operating principle involves a magnetic field interacting with a metal target, typically a toothed wheel or a magnetic ring, which is attached to the shaft. As the shaft rotates, the magnetic field induces a voltage in the target, which is then detected and converted into a digital signal.
The signal is then processed to determine the position or angle of the shaft. The resolution of the encoder is determined by the number of teeth on the wheel or the number of poles in the magnetic ring. The higher the number of teeth or poles, the higher the resolution.
Types of Inductive Encoders
Inductive encoders come in two main types:
Incremental Encoders
Incremental encoders provide a continuous signal that indicates the position of the shaft in small increments. They are commonly used in applications where precise positioning is not required, such as in robotic arms or conveyor belts.
Absolute Encoders
Absolute encoders provide a unique signal for each position of the shaft, allowing for precise determination of the shaft’s position. They are commonly used in applications where precise positioning is critical, such as in machine tools or robotic assembly.
Hybrid Encoders
Hybrid encoders combine the features of incremental and absolute encoders, offering both precise positioning and continuous monitoring of the shaft’s position. They are commonly used in applications where both precise positioning and continuous monitoring are required, such as in robotic welding or cutting machines.
Applications of Inductive Encoders
Inductive encoders have a wide range of applications in various industries, including:
Robotics
Inductive encoders are used in robotic arms, grippers, and conveyor belts to provide precise positioning and control.
Machine Tools
Inductive encoders are used in machine tools, such as lathes, milling machines, and grinders, to provide precise positioning and control of the cutting tool.
Mechatronics
Inductive encoders are used in mechatronic systems, such as motor control systems, pumps, and compressors, to provide precise positioning and control of the moving parts.
Automotive
Inductive encoders are used in various automotive applications, such as in engine management systems, transmission control systems, and brake systems.
Aerospace
Inductive encoders are used in aerospace applications, such as in navigation systems, control systems, and engine management systems.
Benefits of Inductive Encoders
Inductive encoders offer several benefits, including:
High Resolution
Inductive encoders offer high resolution, allowing for precise positioning and control of the shaft.
High Accuracy
Inductive encoders provide high accuracy, ensuring that the shaft is accurately positioned and controlled.
Durability
Inductive encoders are durable and can withstand harsh environments, making them suitable for use in industrial applications.
Low Maintenance
Inductive encoders require minimal maintenance, reducing downtime and increasing productivity.
High Speed
Inductive encoders can operate at high speeds, making them suitable for use in high-speed applications.