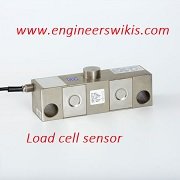
There are several types of load cell sensors available, each with its own design and operating principle. The common types of load cell sensors include:
- Strain Gauge Load Cells: Strain gauge load cells are the most widely used type of load cells. They consist of one or more strain gauges mounted on a metal structure. When a force is applied, the metal structure deforms, causing the strain gauges to change their resistance. This change in resistance is measured and used to calculate the applied force. Strain gauge load cells can be further categorized into:
- Single Point Load Cells: These load cells have a single load application point and are commonly used in bench scales, platform scales, and small weighing applications.
- Shear Beam Load Cells: Shear beam load cells have a rectangular or “S” shape design and are suitable for medium to high capacity weighing applications.
- S-Type Load Cells: S-type load cells have an “S” shape design and are used in tension and compression applications. They offer versatility and are commonly used in hanging scales, crane scales, and force measurement devices.
- Compression Load Cells: Compression load cells are designed to measure compression forces. They are often used in tank weighing, industrial weighing, and force monitoring applications.
- Hydraulic Load Cells: Hydraulic load cells use the principle of fluid pressure to measure force. They consist of a piston and cylinder arrangement filled with hydraulic fluid. When a force is applied, it compresses the fluid, resulting in a pressure change that is measured and converted into a force reading. Hydraulic load cells are known for their high accuracy and ruggedness, making them suitable for heavy-duty applications.
- Pneumatic Load Cells: Pneumatic load cells operate on the same principle as hydraulic load cells, but they use air or gas instead of hydraulic fluid. The force applied to the load cell compresses the air or gas, leading to a pressure change that is measured and converted into a force reading. Pneumatic load cells are often used in applications where hydraulic fluid may not be desirable or practical.
- Capacitive Load Cells: Capacitive load cells use changes in capacitance to measure force. They consist of two parallel plates with a gap between them. When a force is applied, the gap changes, altering the capacitance. The change in capacitance is detected and converted into a force reading. Capacitive load cells are known for their high accuracy, low profile, and resistance to environmental factors such as temperature and humidity.
- Piezoelectric Load Cells: Piezoelectric load cells utilize the piezoelectric effect, where certain materials generate an electric charge when subjected to mechanical stress. The force applied to the load cell generates an electrical charge that is measured and converted into a force reading. Piezoelectric load cells are often used in dynamic force measurement applications, such as impact testing and vibration analysis.
Each type of load cell sensor has its own advantages and suitability for specific applications. The selection of the appropriate load cell depends on factors such as the required capacity, accuracy, environmental conditions, and budget constraints.
The accuracy of a load cell sensor depends on various factors, including the design, construction, and calibration of the load cell, as well as the application-specific requirements. That being said, strain gauge load cells are generally considered to be the most accurate type of load cell sensors.
Strain gauge load cells offer high accuracy and precision due to their design and the use of strain gauges as the primary sensing element. The strain gauges are attached to the load cell structure and measure the deformation caused by the applied force. This deformation is converted into an electrical signal, which is proportional to the applied force.
The accuracy of strain gauge load cells can be further enhanced by using multiple strain gauges in a Wheatstone bridge configuration. This setup helps minimize the effects of temperature variations and compensates for errors caused by factors such as non-linearity and hysteresis.
It’s important to note that the accuracy of a load cell sensor is also influenced by other factors such as proper installation, calibration, and environmental conditions. To achieve the highest accuracy, load cells should be installed and calibrated according to the manufacturer’s guidelines and specifications. Additionally, the load cell’s operating conditions, such as temperature, humidity, and vibration, should be within the specified range to ensure accurate measurements.
Overall, strain gauge load cells, when properly installed, calibrated, and maintained, are widely recognized for their high accuracy and are commonly used in applications where precise force or weight measurements are crucial.