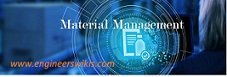
Materials Management
What is Materials Management
Materials Management is simply the process by which an organization is supplied with
the goods and services that it needs to achieve its objectives of
Buying
Storage and
Movement of Materials.
Materials Management is related to –
a. Planning
b. Procuring
c. Storing
d. Providing the appropriate material of
· Right quality
· Right quantity at right place and at the right time.
so as to co-ordinate and schedule the production activity in an integrative way for an
industrial undertaking.
Most industries buy materials, transport them in to the plant, change the materials in to
parts, assemble parts in to finished products, sell and transport the product to the
customer. All these activities of purchase, flow, manufacture, supply and sell the product
at the market requires various types of materials to manage, control their storage, flow
and supply at various places is only possible by efficient Materials Management.
What is the purpose of Materials Management Module
The Goal of materials management is to provide an unbroken chain of components for
production to manufacture goods on time for the customer base. The materials
department is charged with releasing materials to a supply base, ensuring that the
materials are delivered on time to the company using the correct carrier.
Materials generally measured by accomplishing the following task:
On time delivery to the customer
Delivery from the supply base on time
Attaining a freight budget
Inventory shrink management and
Inventory accuracy.
In some companies materials management is also charged with the procurement of
materials by establishing and managing a supply base. In other companies the
procurement and management of the supply base is the responsibility of a separate
purchasing department. The purchasing department is then responsible for the purchased
price variances from the supply base.
How Materials Management Module works
The Department of Materials Management works & provides customers with prompt and
efficient service when a spare part stock or non-stock item is requested. Its main function
is to maintain the stock room and to ensure that the stock room is stocked with the
various parts that a Plant may require.
The Stock Room is inventory of Materials [nothing but money in material form] that
contains all stock types, specialized parts and items.
Non-Stock items such as materials for special work orders. The Department of Materials
Management works with a variety of pre-approved vendors [Approved Vendor List-
AVL] to expedite such special orders.
Material Management along with the other department like
- Production Planning [PP]
- Warehouse Management [WM]
- Finance & Controlling [FICO]
- Sales & Distribution [SD]
- Quality Management [QM]
ensures free flow of materials thereby organizing and streamlining the production
process.