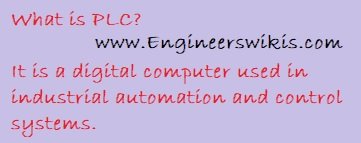
PLC stands for “Programmable Logic Controller.” It is a digital computer used in industrial automation and control systems. PLCs are designed to monitor inputs, make decisions based on a program or logic, and control outputs to automate various processes in industries such as manufacturing, oil and gas, automotive, and more.
PLCs feature a robust and reliable hardware system with input and output modules that connect to sensors, switches, actuators, and other devices in the field. These modules allow the PLC to receive signals from the environment (inputs) and send control signals to actuators and other devices (outputs) to execute specific actions.
The program or logic running on a PLC is typically created using specialized software, often referred to as ladder logic programming. Other programming languages like structured text, function block diagrams, and sequential function charts may also be used depending on the application and the capabilities of the PLC.
PLCs offer several advantages in industrial automation, including:
- Flexibility: PLCs can be easily reprogrammed or modified to adapt to changing process requirements or to accommodate new functionalities.
- Reliability: PLCs are designed to operate in harsh industrial environments and have built-in redundancy features to ensure reliable operation.
- Safety: PLCs can incorporate safety features such as emergency stop circuits and interlocks to protect operators and equipment.
- Scalability: PLCs can be connected in a network to form a distributed control system, allowing for the control of complex processes involving multiple PLCs.
PLCs play a crucial role in the automotive industry by automating and controlling various processes throughout the manufacturing and assembly of vehicles. Here are some common applications of PLCs in the automotive industry:
- Assembly Line Control: PLCs are extensively used to control and coordinate the assembly line operations. They manage the sequencing of tasks, monitor sensors for part presence and positioning, control robots for welding, painting, and assembly, and ensure proper synchronization of all the components involved in the assembly process.
- Conveyor Systems: PLCs are utilized to control conveyor systems within the automotive manufacturing plants. They manage the speed, direction, and timing of conveyors to transport components, sub-assemblies, and finished vehicles between different stages of the production line.
- Quality Control: PLCs are employed for quality control applications, such as inspecting and testing components, sub-assemblies, and finished vehicles. They can monitor sensors and perform measurements to ensure that products meet the specified criteria, triggering alarms or rejecting faulty items.
- Machine Control: PLCs are used for controlling various machines and equipment in automotive manufacturing, including robotic arms, welding machines, painting booths, hydraulic presses, stamping machines, and CNC (Computer Numerical Control) machines. PLCs enable precise control and coordination of these machines to ensure accurate and efficient operations.
- Material Handling: PLCs are deployed to control and optimize material handling systems in automotive plants. This includes managing automated guided vehicles (AGVs) for transporting materials, controlling lifts and conveyors for loading and unloading operations, and monitoring inventory levels.
- Energy Management: PLCs help in monitoring and optimizing energy consumption in automotive manufacturing facilities. They can control lighting systems, HVAC (Heating, Ventilation, and Air Conditioning) systems, and other energy-consuming equipment to ensure efficient operation and reduce energy wastage.
- Safety Systems: PLCs are utilized for implementing safety systems in automotive plants. They can control safety features such as emergency stop buttons, safety interlocks, and safety curtains that ensure the protection of workers and prevent accidents in hazardous areas.