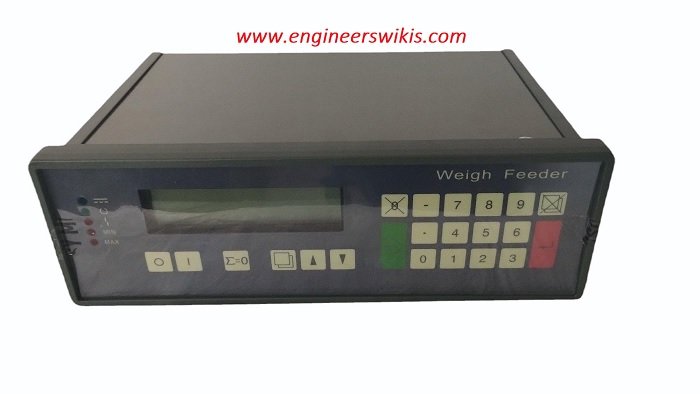
A weigh feeder controller, also known as a weighing controller or weighing feeder controller, is a specialized device used in weigh feeder systems. Weigh feeders are designed to continuously control and monitor the flow rate of bulk materials, such as powders, granules, or solid particles, by weight. The weigh feeder controller performs several functions to ensure accurate and reliable material feed. Here are some key features and functions of a weigh feeder controller:
- Weight Measurement and Control: The weigh feeder controller receives weight signals from load cells or other weighing sensors installed in the weigh feeder system. It continuously measures the weight of the material being fed and provides real-time weight information.
- Speed Control: The controller regulates the speed of the feed mechanism, such as a belt conveyor or screw feeder, to control the material flow rate. It adjusts the speed based on the desired setpoint or target weight, ensuring a consistent and accurate feed rate.
- Setpoint Configuration: The weigh feeder controller allows operators to configure setpoints for the desired feed rate or weight. The setpoint can be adjusted based on production requirements, recipe changes, or specific process parameters.
- Calibration and Taring: The controller facilitates calibration procedures to ensure accurate weight measurements. It may include features for zero calibration, span calibration, and tare adjustment to compensate for the weight of the empty feeder or other system components.
- Material Database: Some weigh feeder controllers have a material database where operators can store and manage information about different materials being fed. This database may include material properties, density values, target weights, and other parameters specific to each material.
- Alarms and Diagnostics: The controller monitors the weigh feeder system for any deviations from the setpoints or abnormal conditions. It can generate alarms or alerts for issues such as over/underfeeding, blockages, or component failures. Diagnostic features may assist in troubleshooting and identifying potential problems in the system.
- Communication and Integration: Weigh feeder controllers often offer communication interfaces, such as serial ports, Ethernet, or fieldbus connectivity, to integrate with plant control systems or supervisory control and data acquisition (SCADA) systems. This enables data exchange, remote monitoring, and control of the weigh feeder system.
- Data Logging and Reporting: The weigh feeder controller can log weight data over time, allowing operators to analyze historical trends and performance. It may generate reports, graphs, or charts for production monitoring, quality control, and compliance purposes.
Weigh feeder controllers are essential components in industries such as mining, cement, chemical processing, food processing, and power generation, where accurate and controlled material feeding is critical. They ensure precise material flow rates, optimize production efficiency, and contribute to consistent product quality.