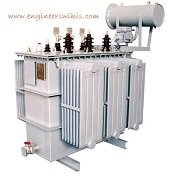
Testing and maintenance are essential aspects of ensuring the reliable and efficient operation of transformers. Transformers play a vital role in electrical power systems, and any failures or malfunctions can have significant consequences. Here are some considerations for transformer testing and maintenance:
- Routine Inspections: Regular visual inspections are necessary to identify any signs of physical damage, overheating, leaks, or other visible issues. Inspecting the transformer’s exterior, cooling system, bushings, and connections can help detect potential problems early on.
- Electrical Testing: Various electrical tests can be performed to assess the transformer’s condition. These tests include turns ratio measurement, insulation resistance measurement, winding resistance measurement, and impedance tests. These tests provide important data on the transformer’s performance and can help identify faults or deterioration.
- Dissolved Gas Analysis (DGA): DGA involves analyzing the gases dissolved in the transformer oil. Faults such as overheating, arcing, or insulation degradation can produce characteristic gases. Regular DGA tests can detect and identify potential faults or abnormal operating conditions within the transformer.
- Oil Analysis: Transformer oil analysis helps assess the condition of the insulation and detects any potential contamination or degradation. It involves analyzing the physical and chemical properties of the oil, including acidity, moisture content, dielectric strength, and presence of contaminants.
- Thermography: Infrared thermography is a non-destructive testing technique used to detect abnormal temperature variations in transformers. Hotspots can indicate loose connections, overloaded circuits, or other issues. Regular thermographic inspections can identify potential problems and prevent failures.
- Bushing Inspections: The bushings provide electrical insulation and support for the conductors entering or exiting the transformer. Regular inspections, including visual examination and electrical testing, help ensure their integrity and detect any signs of damage or deterioration.
- Maintenance Procedures: Depending on the transformer type and application, maintenance procedures may include cleaning, tightening connections, replacing gaskets or seals, repairing or replacing damaged components, and oil filtration or replacement. Manufacturer guidelines and industry standards should be followed for maintenance activities.
- Monitoring Systems: Implementing continuous monitoring systems, such as temperature monitoring, load monitoring, and online DGA, can provide real-time data on transformer performance and enable early detection of abnormalities or faults.