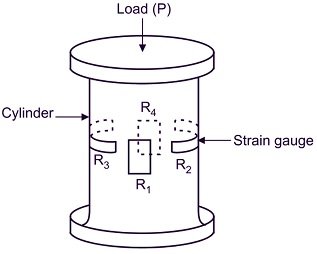
Strain gauge load cells are a type of force transducer used to measure the force or load applied to an object. They are commonly employed in various industries and applications where precise force measurement is required, such as weighing scales, industrial automation, material testing, and process control. Here’s how strain gauge load cells work:
Principle of Operation:
Strain gauge load cells operate based on the principle of the strain effect. When a force or load is applied to the load cell, it deforms slightly, causing strain in the load cell’s internal components. This strain is detected and measured using strain gauges, which are thin, flexible, and highly sensitive elements bonded to the load cell structure.
Strain Gauge Configuration:
Strain gauges are typically arranged in a Wheatstone bridge configuration on the load cell. A Wheatstone bridge consists of four strain gauges connected in a bridge circuit, where two gauges are in tension (positive strain) and two are in compression (negative strain) when the load is applied. This configuration allows for a more accurate and balanced measurement of strain.
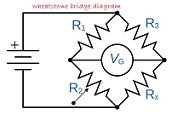
Strain Measurement:
As the load cell deforms under the applied force, the strain gauges also experience strain and undergo a change in electrical resistance. This change in resistance is directly proportional to the applied force and can be measured using a bridge circuit and appropriate instrumentation. The electrical output from the Wheatstone bridge is usually a small voltage signal, which is amplified and processed to obtain the force measurement.
Calibration and Sensitivity:
Strain gauge load cells need to be calibrated to establish a linear relationship between the applied force and the electrical output. Calibration involves applying known forces to the load cell and recording the corresponding output readings. This data is used to create a calibration curve or equation for accurate force measurement. Sensitivity refers to the amount of electrical output change per unit of applied force and is determined during the calibration process.
Types of Strain Gauge Load Cells:
There are different designs of strain gauge load cells, including:
- Compression Load Cells: These load cells are designed to measure compressive forces. They typically consist of a cylindrical or pancake-shaped structure, and the force is applied along the central axis.
- Tension Load Cells: These load cells are used to measure tensile forces. They are designed to have a central opening or threaded ends to accommodate the attachment of the load.
- Beam Load Cells: Beam load cells feature a beam-shaped structure, usually with strain gauges bonded on the top and bottom surfaces. They are commonly used in weighing scales and other applications requiring high accuracy.
- S-Type Load Cells: S-type load cells have an S-shaped structure and are suitable for both tensile and compressive force measurement. They provide good accuracy and are often used in industrial applications.
Advantages of Strain Gauge Load Cells:
- High accuracy and precision in force measurement.
- Wide range of load capacities available.
- Compact size and easy installation.
- Good linearity and repeatability.
- Suitable for both static and dynamic force measurement.
Limitations of Strain Gauge Load Cells:
- Temperature sensitivity: Strain gauge load cells can be affected by temperature changes, requiring temperature compensation techniques for accurate measurements.
- Susceptibility to overloading: Overloading the load cell beyond its rated capacity can result in permanent damage or affect the accuracy of subsequent measurements.
- Vulnerability to external forces: Strain gauge load cells can be sensitive to external forces such as bending, torsion, and side loads, which may introduce measurement errors if not properly accounted for.
Overall, strain gauge load cells are widely used in industrial applications due to their accuracy, reliability, and versatility in measuring forces and loads. Proper installation, calibration, and consideration of environmental factors are essential for obtaining accurate and consistent measurements.