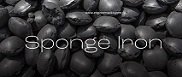
Sponge Iron – Manufacturing Process
The reduction of Iron Ore can be achieved by using carbon bearing material, as non-coking coal or suitable reducing gas in the form of reformed natural gas. The processes employing coal known as solid-reluctant of coal-based processes. Those employing reducing gases known as gas-based processes. Sponge Iron produced by gas-based process is normally hot briquette and hence also known as Briquetted Iron (HBI).
In the decade 1990-2000 the total sponge iron production was as follows:
Gas-Based | : | 4 Million Tonnes |
Coal-Based | : | 3 Million Tonnes |
Coal-Based Process
» | This process utilizes non-coking coal as reducing agent along with lumpy rich grade iron ore. |
» | The reduction is carried out in an inclined horizontal rotary kiln, which rotates at a predetermined speed. A temperature profile ranging from 800-1050 degree centigrade is maintained along the length of the kiln at different zones and as the material flows down due to gravity the ore is reduced. |
» | The hot reduced sponge iron along with semi-burnt coal, discharged from kiln is cooled in water-cooled cylindrical rotary cooler to a temperature of 100–200 degree centigrade. |
» | The discharge from cooler consisting of sponge iron, char other contaminations are passed on through magnetic separators so that sponge iron can be separated from other impurities. |
» | Later the sponge iron is screened into two size fractions i.e. –3 mm & +3 mm. +3 mm fraction directly goes for usage, -3 mm fraction can be either used directly where ever it is possible or is to be briquetted by using molasses and hydrated lime as binders. |
The basic reactions in this process is as follows:
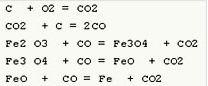
Raw Material Requirements
As in process, here also quality of raw materials plays a vital role in obtaining the rated capacity and quality. The iron ore shall have resistance for physical & thermal decrepitation and good reducibility. The coal should be of reactive nature along with the characteristics of high fusion temperature and less amount of ash.
» Chemical and Physical Composition of Iron Ore
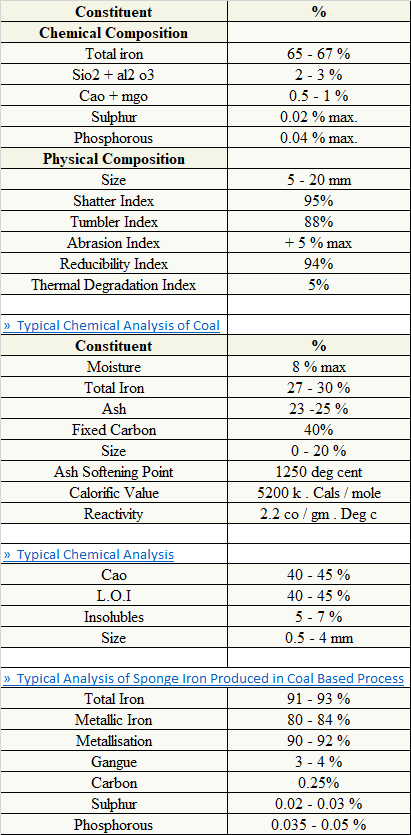
Gas-Based Process
» | This process utilizes natural gas the reducing agent. |
» | Natural gas is reformed to enrich with H2 and Co mixture and this enriched and reformed gas mixture is preheated in gas-based process. |
» | A vertical retort is used for the reduction of iron ore as against a rotary kiln in coal based sponge iron process. |
» | When the gases are traveling upwards the charge moves downward by gravity. |
» | Gas-based sponge iron is not subjected for magnetic separation, as no contamination with non–magnetic is possible either it can be cooled indirectly or briquetted in hot condition to get hot briquetted iron (HBI). |
The basic reactions are as follows:
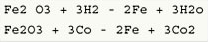
Two well established processes:
1. Midrex
2. Hyl
In gas-based process more preferable feed is pellets. Lump ore used with proper size distribution for required permeability.
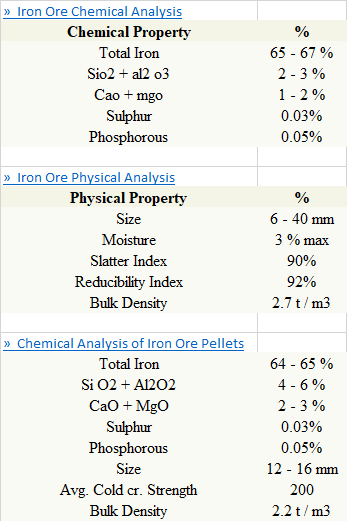
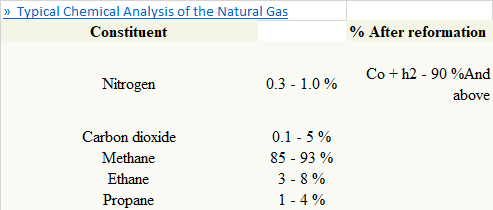
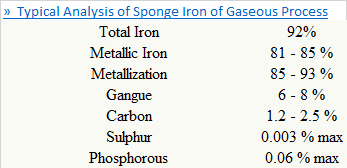
Coal-Based Process v/s Gas-Based Process
» | The present output of sponge iron in India is about 7 MT/year. Out of which 50 % output is based on non–coking coal. |
» | Out of the 73 DRI units in India, 70 units are coal-based and the rest 3 are gas-based. Further the capital cost for setting up of coal-based units is cheaper compared to Gas-based units. Gas deposits are not fully explored and more over allocation of this industry is yet to be demarcated by the government. |
» | DRI, nowadays used along with the scrap as a dilutants of tramp elements and also in some cases as complete feedstock instead of scrap. |
» | It is cheaper, clean and rosily available raw material for making clean steel. |
» | Therefore DRI of coal-based process is of much relevance to steel manufacturing. |
» Comparison between Coal and Gas Based Product
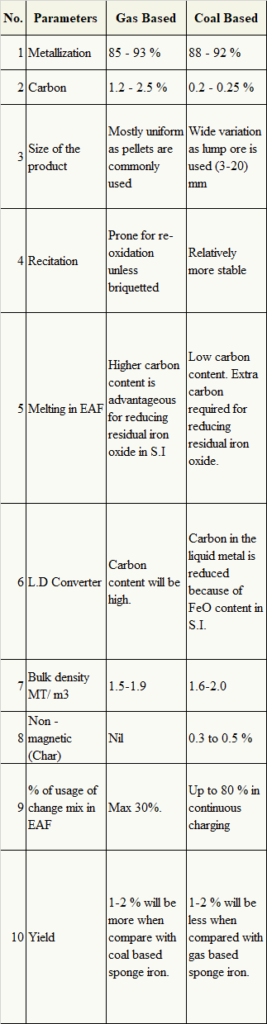