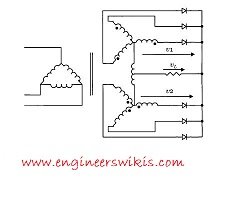
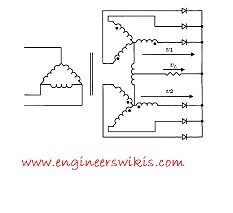
Rectifier transformers are specialized transformers used in high-voltage direct current (HVDC) systems to convert AC (alternating current) power into DC (direct current) power. They play a crucial role in HVDC transmission systems, enabling the efficient and reliable conversion of power over long distances.
The design of a rectifier transformer involves several important considerations to ensure optimal performance and reliability. Here are some key factors to take into account during the design process:
- Voltage and Power Rating: Determine the required voltage and power rating of the rectifier transformer based on the specific HVDC system requirements. This includes considering the AC voltage level, DC voltage level, and power capacity of the system.
- Core Design: Select the appropriate core material and design to achieve the desired magnetic characteristics and minimize core losses. Commonly used core materials include laminated iron cores or amorphous metal cores, which offer reduced core losses.
- Winding Design: Design the primary and secondary windings to withstand the high voltage and current levels involved in the rectification process. Consider the number of turns, conductor size, insulation materials, and cooling provisions to ensure safe and efficient operation.
- Cooling System: Adequate cooling is crucial to maintain the transformer’s temperature within acceptable limits. Design an efficient cooling system, such as oil or water cooling, with appropriate cooling channels or radiators to dissipate heat generated during operation.
- Insulation Design: Select and design the insulation system to withstand the high voltage stresses and ensure electrical reliability. This includes choosing suitable insulation materials, insulation thickness, and insulation coordination to prevent electrical breakdown.
- Harmonic Mitigation: HVDC systems generate harmonics due to the rectification process. Incorporate measures to mitigate harmonics, such as using zig-zag or delta-star windings, providing appropriate filtering, or employing phase-shifting techniques.
- Overload and Short-Circuit Protection: Incorporate protective devices, such as temperature sensors, pressure relief devices, and Buchholz relays, to detect and mitigate overloads or short circuits that may occur during operation.
- Mechanical Considerations: Consider mechanical aspects, such as structural design, support systems, and transportation requirements, to ensure the transformer can withstand mechanical stresses, vibrations, and environmental conditions.
- Standards and Regulations: Adhere to relevant industry standards, codes, and regulations governing transformer design, safety, and performance, such as IEC, IEEE, or specific HVDC system standards.
How can harmonics be mitigated in rectifier transformer design?
Harmonics can be effectively mitigated in rectifier transformer design through various techniques. Here are some commonly used methods:
- Zig-Zag or Delta-Star Windings: Implementing zig-zag or delta-star (also known as “wye”) windings in the transformer can help reduce harmonics. These winding configurations distribute the harmonic currents among multiple windings, thus minimizing their impact on the system.
- Filtering Systems: Install filtering systems, such as harmonic filters or passive filters, to attenuate harmonic currents. Harmonic filters consist of reactive components (such as capacitors and inductors) tuned to the specific harmonic frequencies, allowing them to absorb or redirect the harmonic currents away from the transformer.
- Phase-Shifting Transformers: Introduce phase-shifting transformers into the system to control the harmonic content. By adjusting the phase angle between the primary and secondary windings of the transformer, the harmonic currents can be significantly reduced or canceled out.
- Transformer Taps and Connections: Utilize tap changers and connections to adjust the transformer’s voltage ratio and impedance, which can help mitigate harmonics. By optimizing the tap settings, it is possible to minimize the voltage distortion caused by harmonics.
- Active Harmonic Filters: Employ active harmonic filters that actively monitor the harmonic currents and inject compensating currents of opposite polarity to cancel out the harmonics. Active harmonic filters are capable of dynamically adapting to changing harmonic conditions and providing effective harmonic mitigation.
- Proper Sizing and Design: Ensure that the rectifier transformer is adequately sized to handle the expected harmonic currents without exceeding its rated capacity. Proper consideration of current-carrying capacity, conductor size, and cooling provisions during the design stage can help mitigate harmonics.
- Harmonic Study and Analysis: Conduct a detailed harmonic study and analysis of the HVDC system to identify potential harmonic sources and their characteristics. This information can guide the design process and help determine the most appropriate mitigation methods for the specific harmonic profile.