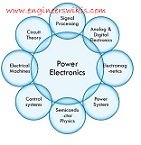
Power electronics thermal management refers to the strategies and techniques employed to manage the heat generated in power electronic systems. Power electronic devices, such as transistors, diodes, and integrated circuits, can generate significant amounts of heat during operation due to power losses and switching activities. Proper thermal management is crucial to ensure the reliable and efficient operation of power electronic systems. Here are some key aspects and techniques involved in power electronics thermal management:
- Heat Sink Design: Heat sinks are commonly used in power electronic systems to dissipate heat from high-power components. Heat sinks provide a larger surface area to facilitate heat transfer and are typically made of materials with high thermal conductivity, such as aluminum or copper. Proper heat sink design, including fin geometry, size, and airflow considerations, is essential for effective heat dissipation.
- Thermal Interface Materials (TIMs): TIMs are used between power electronic devices and heat sinks to enhance heat transfer by filling gaps and irregularities. These materials, such as thermal greases, thermal pads, or phase change materials, help improve the thermal contact between the device and the heat sink, reducing thermal resistance and enhancing heat dissipation.
- Forced Air Cooling: Forced air cooling involves using fans or blowers to circulate air across heat sinks or components to enhance heat dissipation. Airflow can be directed using ducts or channels to ensure effective cooling. Forced air cooling is commonly used in applications where natural convection is insufficient to handle the heat dissipation requirements.
- Liquid Cooling: Liquid cooling techniques involve circulating a coolant, typically water or a mixture of water and glycol, through a heat exchanger or cold plate in contact with power electronic devices. Liquid cooling offers higher heat transfer coefficients compared to air cooling, enabling more efficient heat dissipation. It is particularly useful in high-power and high-temperature applications.
- Thermal Management Systems: Advanced thermal management systems employ sensors and control algorithms to monitor the temperature of power electronic components and adjust cooling mechanisms accordingly. These systems can regulate fan speeds, control pump operations in liquid cooling systems, or adjust power levels to maintain optimal operating temperatures and prevent overheating.
- Thermal Analysis and Simulation: Thermal analysis and simulation tools help in predicting and optimizing the thermal performance of power electronic systems. These tools utilize computational fluid dynamics (CFD) and finite element analysis (FEA) techniques to model heat flow, temperature distribution, and airflow patterns. By simulating different thermal management strategies, designers can optimize the system’s thermal performance before implementation.
- Thermal Protection and Safety Measures: Thermal protection features, such as temperature sensors, thermal shutdown circuits, and alarms, are implemented to prevent overheating and protect power electronic components from thermal damage. These safety measures ensure the reliable and safe operation of the system.
- Component Placement and Layout: Proper placement and layout of power electronic components within the system can significantly impact thermal management. Designers should consider factors such as proximity to heat sinks, airflows, and avoiding hotspots to optimize heat dissipation and minimize temperature gradients.
Effective thermal management in power electronics is crucial to maintain component reliability, prevent thermal-induced failures, and optimize the system’s efficiency. By employing appropriate cooling techniques, efficient heat sink designs, and thermal analysis tools, engineers can ensure that power electronic systems can operate within safe temperature limits and deliver optimal performance.
What are some common thermal management challenges faced in power electronic systems?
Thermal management in power electronic systems presents several challenges due to the high power densities, switching frequencies, and compact designs of these systems. Some common thermal management challenges faced in power electronic systems include:
- High Power Density: Power electronic systems often operate at high power densities, which means a significant amount of heat is generated in a relatively small space. Managing and dissipating this heat effectively becomes challenging as it can lead to temperature rise, thermal stress, and reduced reliability of components.
- Limited Space: Power electronic systems are often designed with limited space, particularly in applications such as electric vehicles, portable devices, or densely packed electronic enclosures. The compact size restricts the available area for heat sinks, cooling mechanisms, and airflow, making it challenging to achieve efficient heat dissipation.
- Transient Operation: Power electronic systems experience transient operations, where the power levels and thermal loads can change rapidly. These transient conditions can lead to temperature spikes and thermal cycling, which can affect the reliability and lifespan of components. Ensuring thermal management under varying operating conditions is a challenge.
- Switching Frequencies: Power electronic devices operate at high switching frequencies, which can exacerbate thermal management challenges. Rapid switching leads to increased power losses and heat generation, requiring effective heat dissipation techniques to prevent excessive temperature rise.
- Thermal Interactions: In power electronic systems, heat generated by one component can impact the thermal performance of neighboring components. Thermal interactions and hotspots can occur, leading to localized temperature rise and possible thermal runaway if not properly managed.
- Non-Uniform Heat Distribution: Power electronic systems often have non-uniform heat distribution due to variations in power dissipation across components or uneven airflow patterns. Non-uniform heat distribution can result in localized hotspots, temperature gradients, and thermal stress, which can degrade component performance and reliability.
- Environmental Conditions: Power electronic systems may operate in harsh environmental conditions, such as high ambient temperatures, dusty environments, or confined spaces. These conditions can further exacerbate thermal management challenges and require robust cooling mechanisms to maintain optimal operating temperatures.
- Reliability and Lifetime Considerations: Overheating can significantly impact the reliability and lifespan of power electronic components. Excessive temperatures can cause accelerated aging, thermal fatigue, and thermal-induced failures in devices such as semiconductors, capacitors, and connectors. Ensuring adequate thermal management is crucial to extend the system’s operational lifetime.