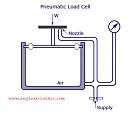
Pneumatic load cells are a type of force transducer that use compressed air or gas to measure the force or load applied to an object. They are commonly used in various industrial applications where high load capacities, fast response times, and resistance to harsh environments are required. Here’s how pneumatic load cells work:
Principle of Operation:
Pneumatic load cells operate based on the principle of Boyle’s law, which states that the pressure of a gas is inversely proportional to its volume when the temperature is kept constant. The load cell consists of a chamber filled with compressed air or gas and a diaphragm or piston that is subjected to the applied force. The force causes a change in the volume of the gas, resulting in a corresponding change in pressure, which is then converted into an electrical signal for measurement.
Pneumatic System Configuration:
The load cell contains a chamber filled with compressed air or gas, typically provided by an external air supply system. The diaphragm or piston, known as the sensing element, is exposed to the force being measured. As the force is applied, it causes the sensing element to deform, resulting in a change in the volume of the gas inside the chamber.
Pressure Measurement:
The change in volume of the gas corresponds to a change in pressure within the load cell. This pressure is measured using a pressure transducer or a pressure gauge connected to the load cell. The pressure measurement is converted into an electrical signal, usually through an analog or digital interface, for further processing and analysis.
Calibration and Sensitivity:
Pneumatic load cells need to be calibrated to establish a linear relationship between the applied force and the measured pressure. Calibration involves applying known forces to the load cell and recording the corresponding pressure readings. This data is used to create a calibration curve or equation for accurate force measurement. Sensitivity refers to the change in pressure per unit of applied force and is determined during the calibration process.
Advantages of Pneumatic Load Cells:
- High load capacity: Pneumatic load cells can handle large load capacities, ranging from a few kilograms to several hundred tons, making them suitable for heavy-duty applications.
- Fast response time: Pneumatic load cells have a rapid response time, allowing for real-time force measurement and monitoring in dynamic applications.
- Insensitivity to external factors: Pneumatic load cells are less affected by external factors such as temperature variations, electromagnetic interference, and vibrations, ensuring stable and reliable measurements in challenging environments.
- Overload protection: Pneumatic load cells have built-in overload protection capabilities. The compressibility of the gas acts as a cushioning medium, absorbing any sudden or excessive loads and preventing damage to the load cell.
- Resistance to harsh environments: Pneumatic load cells are designed to withstand harsh conditions, including high temperatures, moisture, and corrosive environments. They are often constructed with robust materials such as stainless steel to ensure durability.
Limitations of Pneumatic Load Cells:
- Maintenance requirements: Pneumatic load cells require periodic maintenance, including checking for leaks, ensuring proper gas supply, and calibration, to ensure accurate and reliable measurements over time.
- External gas supply: Pneumatic load cells rely on an external gas supply system, which adds complexity and requires proper setup and maintenance.
- Limited accuracy: Compared to some other load cell technologies, pneumatic load cells may have slightly lower accuracy levels, especially in applications requiring high precision force measurements.
Pneumatic load cells are commonly used in industries such as automotive, aerospace, material handling, and industrial automation. They provide accurate force measurements in demanding environments and are suitable for applications such as weighing systems, force testing, machine monitoring, and process control.