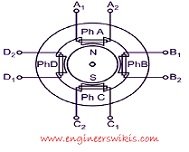
A permanent magnet motor, also known as a PM motor or a brushless DC motor (BLDC), is a type of electric motor that uses permanent magnets embedded in the rotor to generate the magnetic field required for operation. Unlike induction motors, PM motors do not rely on induced currents in rotor windings to create a magnetic field. Here are some key points about permanent magnet motors:
- Working Principle: Permanent magnet motors operate based on the interaction between the magnetic fields of the stator and the rotor. The stator contains the stationary windings, typically arranged in a three-phase configuration, which generate a rotating magnetic field when supplied with current. The rotor contains permanent magnets that produce a magnetic field. The interaction between the rotating magnetic field of the stator and the fixed magnetic field of the rotor generates torque, causing the rotor to rotate.
- Permanent Magnets: The rotor of a PM motor incorporates permanent magnets made of materials with high magnetic coercivity, such as neodymium (NdFeB) or samarium cobalt (SmCo). These magnets retain their magnetic properties without the need for an external power source.
- Brushless Design: PM motors are often referred to as brushless motors because they do not require brushes and commutators for operation. Instead, they utilize electronic commutation through sensors or sensorless algorithms to control the timing and phase of the stator current, ensuring proper rotation.
- Efficiency and Power Density: Permanent magnet motors are known for their high efficiency and power density. The absence of rotor windings reduces losses associated with resistance, resulting in improved efficiency. The use of permanent magnets in the rotor also allows for a compact and lightweight motor design.
- Speed Control: PM motors are typically controlled using electronic motor drives, such as motor controllers or inverters, which regulate the voltage and frequency of the applied power to control the motor’s speed and torque. This electronic control enables precise and variable speed control for different applications.
- Applications: Permanent magnet motors find applications in various industries and devices, including electric vehicles (EVs), hybrid vehicles (HEVs), industrial automation, robotics, HVAC systems, computer hard drives, and more. Their high efficiency, compact size, and controllability make them suitable for a wide range of applications.
Here are some common applications of permanent magnet motors:
- Home appliances – Small home appliances like blenders, food processors, hand mixers often use PMDC or BLDC motors.
- Power tools – Cordless drills, saws, sanders, angle grinders use permanent magnet motors in their battery-powered designs.
- Motorsports – RC cars, helicopters, drones and model aircraft employ lightweight, high-power permanent magnet motors.
- Electric vehicles – EVs, hybrids and plug-in hybrids use PMAC or PMSM motors for propulsion and accessory functions.
- White goods – Clothes washers, dishwashers, refrigerators can use PM motors for pumping and fan applications.
- Factory automation – Precision motion control equipment like stages, gantries use PM motors for high-efficiency operation.
- Medical equipment – Exam tables, dental drills, exercise equipment use PM motors for compact sizes.
- Robotics – Industrial robots, exoskeletons require high torque/power density from PM brushless motors.
- CNC machines – Small machine tools like routers, laser cutters employ PM motors for precise rpm control.
- HVAC equipment – Modern variable-speed blowers and compressors use electronically-commutated PM motors.