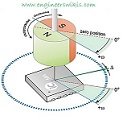
Magnetic encoders are electronic devices used for position sensing and motion control. They utilize magnetic fields and sensors to measure the position, speed, and direction of rotation or linear displacement. Here are some key features and aspects of magnetic encoders:
- Operating Principle: Magnetic encoders consist of a magnetized target or scale and a sensor or sensor array. The target or scale contains magnetic patterns or poles, while the sensor(s) detect the changes in the magnetic field as the target moves. The sensor converts the magnetic field variations into electrical signals, which are then processed to determine position or motion.
- Types of Magnetic Encoders:
- Incremental Magnetic Encoders: These encoders provide information about the position changes relative to a starting point. They generate pulses, typically in the form of quadrature signals (A, B, and sometimes an index signal), which are used to track position, speed, and direction of rotation or linear displacement.
- Absolute Magnetic Encoders: Absolute encoders provide the exact position information without the need for a reference point. They encode the position information in a unique binary or gray code for each position on the scale. This allows direct reading of the absolute position, even after power loss.
- Magnetic Sensing Technologies: Magnetic encoders utilize various sensing technologies, including:
- Hall Effect Sensors: These sensors detect changes in the magnetic field strength using the Hall effect, which is the generation of a voltage proportional to the strength of the magnetic field.
- Magnetoresistive Sensors: Magnetoresistive sensors utilize the magnetoresistive effect, which is the change in electrical resistance based on the strength and orientation of the magnetic field.
- Resolution and Accuracy: Magnetic encoders offer high resolution, allowing precise position or motion measurements. The resolution is determined by the number of magnetic poles or patterns on the scale, and it corresponds to the number of pulses generated or the unique positions encoded. Accuracy depends on factors such as the quality of the scale, sensor, and signal processing electronics.
- Rotary and Linear Encoders: Magnetic encoders are available in both rotary and linear configurations. Rotary encoders are used for measuring rotational motion, such as in motor shafts or robotic joints. Linear encoders are employed for linear displacement measurements, often in applications such as CNC machines, linear actuators, and industrial automation.
- Applications: Magnetic encoders find applications in various industries and systems, including:
- Robotics and automation: For precise control of robotic arms, motor positioning, and feedback control systems.
- CNC machines: To determine the position and movement of cutting tools or workpieces.
- Automotive: In throttle control, steering angle detection, and motor control systems.
- Industrial machinery: For speed control, position feedback, and synchronization in conveyors, motors, and actuators.
- Medical equipment: In imaging systems, robotic surgery, patient positioning, and lab instruments.
- Advantages: Magnetic encoders offer several advantages, including high resolution, accuracy, durability, and immunity to dust, dirt, and moisture. They are also less susceptible to mechanical wear and can operate in harsh environments.
It’s worth noting that there are different types of encoders available, such as optical encoders and capacitive encoders, each with their own advantages and applications. Magnetic encoders are particularly valued for their robustness, reliability, and resistance to environmental conditions in many position sensing and motion control applications.
Applications of Magnetic Encoders:
Below are applications of magnetic encoders:
- Motor Control Systems: Magnetic encoders are widely used in motor control systems, including servo motors, brushless DC motors, and stepper motors. They provide accurate position feedback, enabling precise motor control, speed regulation, and synchronization.
- Robotics and Automation: Magnetic encoders play a crucial role in robotics and automation applications, providing position feedback for precise control of robot arms, joints, and end effectors. They enable accurate positioning, motion control, and path planning in robots.
- CNC Machines: In computer numerical control (CNC) machines, magnetic encoders are used for precise position feedback and control of cutting tools, spindles, and axes. They contribute to high-precision machining operations and repeatability.
- Automotive Systems: Magnetic encoders find applications in various automotive systems, including throttle control, steering angle measurement, transmission control, and suspension systems. They provide accurate position information for safe and efficient vehicle operation.
- Industrial Machinery: Magnetic encoders are utilized in a wide range of industrial machinery, such as conveyors, material handling systems, packaging machines, and printing equipment. They enable accurate position sensing, speed control, and synchronization of moving parts.
- Aerospace and Aviation: Magnetic encoders are employed in aerospace and aviation applications, including flight control systems, navigation systems, and aircraft engines. They provide precise position feedback and control for flight control surfaces, engine components, and rotor systems.
- Medical Equipment: Magnetic encoders find applications in medical equipment, such as imaging systems (CT scanners, MRI machines), robotic surgery systems, and patient positioning devices. They enable accurate positioning, motion control, and feedback in medical applications.
- Renewable Energy Systems: Magnetic encoders are used in renewable energy systems like wind turbines and solar tracking systems. They help track the position and orientation of blades or solar panels, optimizing energy capture and system efficiency.
- Consumer Electronics: Magnetic encoders are employed in various consumer electronics devices, including gaming controllers, audio equipment, and virtual reality systems. They provide accurate position sensing and control, enhancing user experience and interaction.
- Measurement and Metrology: Magnetic encoders are utilized in measurement and metrology applications where precise position measurement is required. They find use in coordinate measuring machines (CMMs), linear stages, and precision measurement tools.