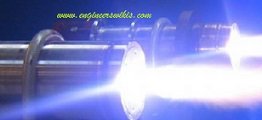
How PLASMA BURNER works
Plasma burners work by utilizing the properties of plasma, a high-temperature ionized gas, to perform various industrial processes such as cutting, welding, and heating.
Following are the step-by-step explanation of how plasma burners operate:
- Gas Flow: The process begins with the flow of a suitable gas, typically compressed air or an inert gas like nitrogen or argon, into the plasma burner. The gas supplied through a gas inlet and regulated by flow control mechanisms.
- Gas Ionization: The flowing gas enters the plasma torch, which contains a narrow nozzle or electrode. As the gas passes through this nozzle or electrode, it encounters a high-frequency electrical current.
- Ionization and Plasma Formation: The high-frequency current provides the necessary energy to ionize the gas. Ionization involves stripping electrons from the gas atoms or molecules, resulting in the formation of a plasma. The plasma, a highly ionized state of matter, consisting of positively charged ions, free electrons, and neutral particles.
- Plasma Arc Formation: The ionized gas, now in the form of a plasma, creates a conductive path for the electrical current. This leads to the formation of a plasma arc, which is a concentrated and intense stream of plasma. The plasma arc sustained by the continuous flow of the ionized gas.
- Heat Generation: The plasma arc generates an enormous amount of heat due to the high temperatures reached by the plasma. Temperatures can range from 10,000 to 30,000 degrees Celsius (18,000 to 54,000 degrees Fahrenheit) depending on the specific application and settings. The heat concentrated within the plasma arc, allowing for precise control and focused application of thermal energy.
- Cutting, Welding, or Heating: The intense heat of the plasma arc directed towards the target material or workpiece. Depending on the application, the plasma burner used for cutting, welding, or heating. For example, in plasma cutting, the heat of the plasma arc melts the metal, while a high-velocity gas jet blows away the molten material, resulting in a clean cut. In welding, the heat of the plasma arc melts the edges of the workpieces, allowing them to fuse together when pressure applied.
- Gas Cooling and Shielding: To protect the plasma torch and ensure stable operation, cooling mechanisms incorporated in the design. These mechanisms circulate cool gas or liquid through the torch to dissipate heat and prevent damage. Additionally, the plasma arc may be surrounded by a shielding gas, such as argon, to protect it from atmospheric contamination and maintain a stable plasma state.
- Controls and Automation: Plasma burners may incorporate control systems, such as computer numerical control (CNC), to automate and precisely control various parameters, including gas flow, arc current, and torch movement. These systems enable consistent and accurate performance, especially in industrial settings where repeatability and precision are crucial.
Here are some additional details about plasma burners:
Plasma Generation Methods
Plasma generated in different ways within a plasma burner. The two common methods are:
- Non-transferred arc: In this method, the plasma arc formed between the electrode (cathode) inside the torch and the nozzle or workpiece (anode) outside the torch. The plasma arc not transferred to the workpiece, but used for processes like plasma cutting and surface treatment.
- Transferred arc: In this method, the plasma arc transferred from the electrode to the workpiece. A pilot arc initially established between the electrode and the nozzle, and then a secondary arc established between the nozzle and the workpiece. This method is commonly used for processes like plasma welding.
Torch Design:
Plasma torches come in various designs, depending on the application and manufacturer. They typically consist of an electrode, a nozzle, cooling channels, gas flow passages, and shielding gas ports. The electrode, usually made of tungsten or hafnium, provides the electrical contact for the plasma arc. The nozzle, often made of copper or a high-temperature alloy, shapes and focuses the plasma arc. Cooling channels and gas flow passages help dissipate heat and maintain the stability of the torch.
Power Supply:
Plasma burners require a power supply to generate and maintain the plasma arc. The power supply provides the necessary electrical current and voltage to ionize the gas and sustain the plasma arc. Depending on the specific application, power supplies can be constant current (CC) or constant voltage (CV), and they may use direct current (DC) or alternating current (AC) sources.
Gas Selection:
The choice of gas used in plasma burners depends on the application and desired properties. Compressed air commonly used as a plasma gas for general cutting and welding processes. Inert gases like nitrogen or argon are used when enhanced control, stability, or protection against oxidation is required. Some applications may also involve the use of specialty gases or gas mixtures to achieve specific results.
Process Control:
Plasma burners can be controlled manually or through automated systems. Manual control involves adjusting parameters such as gas flow, current, and torch movement by the operator. Automated systems, such as CNC, enable precise control over these parameters, allowing for consistent and repeatable results. Automated control systems can also integrate additional features like height sensing, arc voltage control, and process monitoring for enhanced performance.
Advanced Plasma Systems:
Ongoing research and development in plasma technology have led to advancements in plasma burner systems. For instance, some plasma burners incorporate pilot arc technology, where a low-power arc used to initiate the main plasma arc. This improves arc stability and allows for easier ignition, especially in difficult-to-start applications. Additionally, advancements in plasma gas dynamics, torch design, and power supply technology have led to improved efficiency, cut quality, and overall performance.
Industrial Applications:
Plasma burners find applications in various industries, including metal fabrication, automotive, aerospace, electronics, construction, and more. They are used for cutting and welding a wide range of materials, including steel, stainless steel, aluminum, copper, and exotic alloys. Plasma burners are also employed in surface treatment, heat treatment, waste disposal, and other specialized processes.