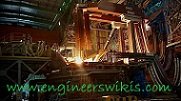
An electric arc furnace (EAF) transformer is a specialized type of transformer used in electric arc furnaces, which are industrial furnaces used for steelmaking. EAF transformers are designed to meet the unique requirements of the EAF process, which involves converting electrical energy into intense heat through an electric arc.
Here are some key features and considerations related to electric arc furnace transformers:
- High Current and Low Voltage: EAF transformers are designed to handle high currents typically ranging from a few thousand to tens of thousands of amperes. They operate at low voltages, typically in the range of a few hundred volts to a few kilovolts.
- High Overload Capability: EAF transformers are designed to withstand high overload conditions, which are common in the EAF process due to the fluctuating arc resistance and varying electrical load. They are built with robust construction and cooling systems to handle these intermittent high-current demands.
- Tap Changers: EAF transformers often incorporate on-load tap changers (OLTC) to adjust the transformer’s secondary voltage during operation. The tap changers allow for fine-tuning of the voltage to match the specific needs of the EAF process.
- Harmonic Mitigation: Electric arc furnaces generate significant harmonic currents due to the non-linear nature of the arc. To mitigate harmonics and prevent their propagation into the power system, EAF transformers may include various harmonic filtering techniques, such as zig-zag or delta-star windings, passive harmonic filters, or active harmonic filters.
- Cooling Systems: EAF transformers require efficient cooling systems to handle the heat generated by the high currents and overloads. Common cooling methods include oil-immersed cooling or water-cooling systems, which ensure the transformer remains within acceptable temperature limits during operation.
- Robust Insulation: EAF transformers are subjected to harsh operating conditions, including high temperatures, mechanical vibrations, and potential exposure to dust and contaminants. Therefore, they are designed with robust insulation systems using materials that can withstand these conditions and maintain electrical integrity.
- Monitoring and Protection Systems: EAF transformers are equipped with comprehensive monitoring and protection systems. These systems include various sensors and relays to monitor parameters such as temperature, oil level, winding currents, and provide protection against faults, overloads, and other abnormal operating conditions.
The design and construction of EAF transformers require expertise in dealing with high currents, harmonics, and the specific requirements of the steelmaking process. Specialized transformer manufacturers and engineers with experience in EAF applications are typically involved in the design and production of these transformers.
What are the common cooling methods used in electric arc furnace transformers?
Electric arc furnace (EAF) transformers require efficient cooling methods to dissipate the heat generated by high currents and overloads. Here are some common cooling methods used in EAF transformers:
- Oil-immersed Cooling: Oil-immersed cooling is one of the most widely used cooling methods for EAF transformers. The transformer windings and core are immersed in a high-quality insulating oil, such as mineral oil or synthetic ester oil. The oil acts as both an insulating medium and a coolant, effectively dissipating heat from the transformer. Heat is transferred from the windings to the oil, and then circulated to cooling radiators or heat exchangers, where it is further dissipated to the surrounding environment.
- Water Cooling: Water cooling is utilized in some EAF transformers, especially for those operating at higher power levels. Water is circulated through cooling channels or pipes embedded within the transformer windings and core. The water absorbs heat from the transformer and carries it away to an external cooling system or a water cooling tower. Water cooling offers higher heat dissipation capacity than oil-immersed cooling and is particularly effective for handling the high thermal loads associated with EAF transformers.
- Forced Air Cooling: Forced air cooling involves the use of fans or blowers to circulate air over the transformer windings and core. Air is drawn from the surroundings and forced through cooling ducts or passages within the transformer. This method promotes heat transfer by convection, carrying away the heat generated by the transformer. Forced air cooling is typically used in smaller EAF transformers or as an auxiliary cooling method in conjunction with oil-immersed or water cooling.
- Combination Cooling: In some cases, EAF transformers employ a combination of cooling methods to meet the cooling requirements. For example, a transformer may utilize oil-immersed cooling for the core and lower-current windings, while employing water cooling for the high-current windings. This combination approach optimizes cooling efficiency and ensures effective heat dissipation across different parts of the transformer.