Control Valves The most common method for influencing the behaviour of chemical processes is through the flow rate of process streams. Usually, a variable resistance in the closed conduit or pipe is manipulated to influence the flow rate and achieve the desired process behaviour. A valve with a variable opening for flow is the standard equipment used to introduce this variable resistance; the valve is selected because it is simple, reliable, relatively low cost and available for a wide range of process applications. In some cases the valve resistance is set by a person adjusting the opening, like a home faucet. In many cases the valve resistance is determined by an automatic controller, with the valve designed to accept and implement the signal sent from the controller. These are control valves. A multitude of commercial control valves are available; so the goal of this section is to describe the key features of common valves and provide guidance on proper selection and sizing. The principles of flow control through a restriction in a pipe are presented in textbooks on fluid mechanics (e.g., Janna, 1993) and are briefly summarized here with reference to the example system in Figure 1 taken from Marlin (2000). Naturally, the total pressure drop along the pipe after the valve is the sum of the individual pressure drops, as given in the following equation. |
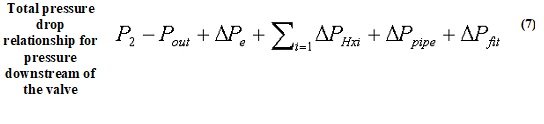
As we know the resistance to fluid flow increases as the flow rate increases. Also, the source of the high pressure, here a pump, may be influenced by the flow rate; in this case, the pump head decreases as the flow increases. The relationship between the pressures at the inlet and exit of the valve are shown in Figure 1, and the required pressure drop across the valve is shown as DPv. Therefore, any desired flow from 0 to 110% of the design valve can be achieved by adjusting the valve opening to provide the required resistance to flow, DPv. For the example in Figure 1, when the flow is 80% of design, the valve pressure drop is about 40 psi, which can be achieved by adjusting the valve opening for flow to the proper value.
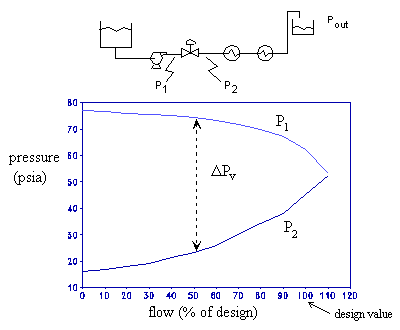
Note that energy is required to raise the stream pressure to P1 is “lost energy”. Therefore, efficient design minimizes the valve pressure drop while providing sufficient variable resistance for good flow regulation. Theoretically, a control valve would not be needed if the supply pressure, in Figure 1 this is P1, could be varied. Variable speed electrical motors to drive pumps are available for liquid systems, but the added cost and lower efficiencies of these pumps has resulted in the control valve remaining the standard choice for regulating liquid flow (Bauman, 1981). Variable speed steam turbines to drive compressors are commonly applied for gas systems; thus, two methods for adjusting flow in gas systems are common in the process industries: these are:
- Manipulating the supply pressure (by the speed of the compressor or pump) and
- Manipulating the variable flow resistance (by a control valve).
We will concentrate on control valves, which are the overwhelming choice for flow control in the process industries.
Issues in Valve Selection |
Valves are used extensively for affecting the process; we often say that values are the “handles” by which we operate a process. We have many goals in influencing the process; therefore, we use the flow and valve principles in many applications. There are many types of valves. The four most prominent types of valves are summarized below.
Table 1. Most common applications of valves in the process industries.
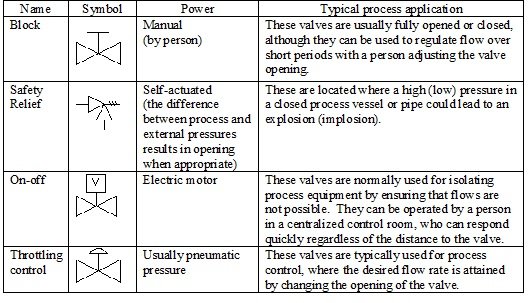
Properly operating valves are essential for safe and profitable plant operation. Valve selection can be guided by the analysis of a set of issues, which are presented in this section. Each issue is introduced here with process examples, and details on the issues are provided in the remainder of this site for the most common valves in the process industries.
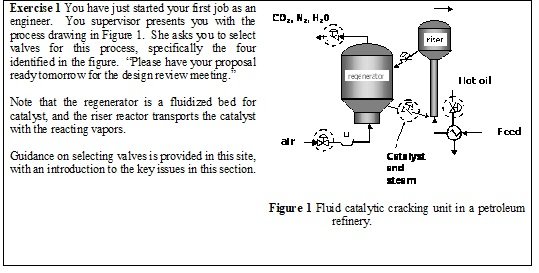
When defining valve requirements and principles, the engineer should use terminology that has a unique meaning, which is not easily achieved. Therefore, the engineer should refer to accepted standards and use the terminology provided in the standards. For instrumentation, standards published by the ISA (formerly, Instrument Society of America) are the most relevant. This section uses terms from the ISA wherever possible.
1 Major issues for selecting valves
The major issues in valve selection are summarized in the following. The relative importance of each issue depends upon the specific application; for example, one application might require a low pressure drop, while another might require a large range. Generally, we find that the greater the requirements for good performance, the higher the cost for purchase and maintenance. Therefore, we must find the proper balance of performance and cost, rather than always specify the best performing valve.
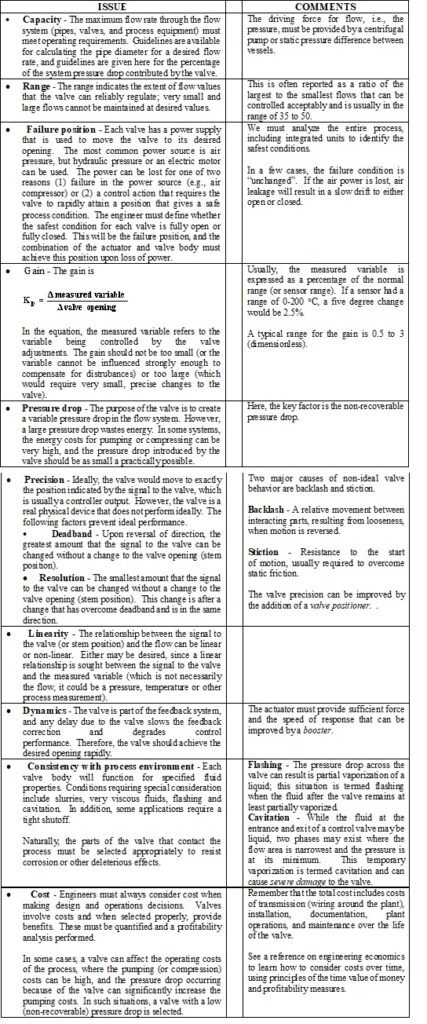
Currently, valve technology is experiencing a dramatic change. While the basic physics of valves is not changing, valves are being enhanced by the addition of microprocessors at the location of the positioner/actuator. This change makes the following features possible that were not available with older technologies. The following assumes a digital valve positioner.
· Digital conversion and transmission – The “signal” from the controller is no longer an analog signal (typically 4-20 mA). The signal can be digital, with many controller outputs transmitted by a single digital transmission. This substantially reduces the cable costs. The signal is converted to an analog pneumatic value for the valve actuator at the control valve.
· Diagnostics – The valve can provide sophisticated diagnostics of its performance. For example, excessive backlash or stiction can be identified and reported to the centralized control room. Then, maintenance can be performed before the valve performance degrades to the point of reducing process performance.
Control Valve Body |
Many types of valve bodies are available to achieve specific flow regulation behaviour. The following description addresses the main valve bodies used in the process industries; key features of each body type are presented after the descriptions in Table below.
Globe Valve: The name “globe” refers to the external shape of the valve, not the internal flow area. A typical globe valve has a stem that is adjusted linearly (up and down) to change the position of the plug. As the plug changes, the area for flow between the plug and seat (opening) changes. Many different seat and plug designs are available to achieve desired relationships between the stem position and flow rate; see the discussion on valve characteristic below. The standard plug must oppose the pressure drop across the valve, which is acceptable for small pressure drops. For large pressure drops, a balanced globe valve is used to enable a valve with small force to open and close the plug.
Ball: The restriction for this body is a solid ball which has some part of the ball removed to provide an adjustable area for flow. The ball is rotated to influence the amount of flow. The example ball valve displayed through the link below has a tunnel through the ball, and the ball is rotated to adjust the fraction of the tunnel opening available for flow. Other types of ball valves have different sections removed from the ball to give desired properties.
Butterfly: The butterfly valve provides a damper that is rotated to adjust the resistance to flow. This valve provides a small pressure drop for gas flows.
Diaphragm: The diaphragm valve has one surface which is deformed by the force from the valve stem to vary the resistance to flow.
Gate: These valves have a flat barrier that is adjusted to influence the area for flow. These bodies are used primary for hand-operated valves and valves automated for emergency shutoff.
Table.2 Summary of Features for Selected Control Valve Bodies
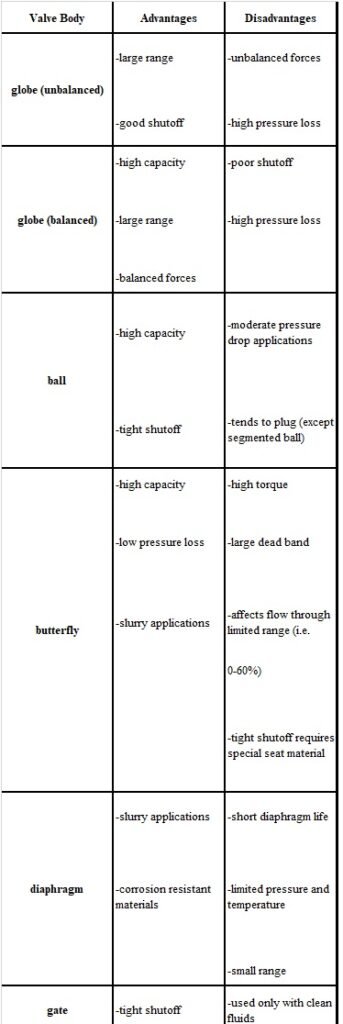
Valve Characteristic |
The relationship between the valve stem position and the flow is defined as the valve characteristic. This relationship with constant (design value) pressure drop is termed the inherent characteristic, and the relationship in a specific process in which the pressure drop may vary with flow is termed the installed characteristic. Two related units are used for the characteristic; one is flow in gallons of water per minute per stem percent that is used for sizing control valves. The other is percent maximum flow per stem percent which is used to plot typical valve characteristics.
The flow through a restriction can often be represented by

With, in this expression, the characteristic expressed as a percentage of the maximum flow, and Fmax is the maximum flow rate with a pressure drop of 1 psi.
A wide range of functional relationships for the Cv can be implemented through the detailed design of the shapes of the plug and seat. Some typical characteristics are shown in Figure 2. The valve characteristic relationship is usually selected to provide a nearly linear relationship between the stem positions, which should be the controller output sent to the valve, and the controlled variable. If this goal is achieved, constant controller tuning will be appropriate for the entire range of controller output (and flow rate). To achieve this goal for a process with a constant process gain , a linear characteristic is appropriate, and when the process gain changes with
flow rate, the valve characteristic should be the inverse of the process non-linearity.
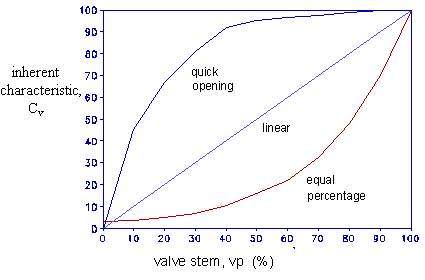
The straightforward procedure for determining a linearizing characteristic is explained in many references, e.g., Marlin (2000) Section 16.5. While some references suggest guidelines for the application of characteristics to specific process applications, the procedure in Marlin (2000) is easy to perform and recommended.
Also, note that linearizing the control loop is not always the most important goal. For example, a valve that must increase the flow from zero rapidly to protect equipment should have a quick opening characteristic, even if this contributes to a nonlinear feedback loop.
Valve Sizing |
Control valve sizing involves determining the correct valve to install from the many valves commercially available. The procedure is based on information provided by valve manufacturers, who specify the capacity of their valves using the valve coefficient, Cv. The valve coefficient is defined as the flow of water that will pass through the valve when fully open with a pressure drop of 1 psi. In these tables, the units of Cv are gallons of water per minute per psi1/2. The engineer must calculate the desired Cv for the process fluid and conditions by applying appropriate correction factors and select the valve using tables of Cv versus valve stem position and line size provided by the manufacturers
The required flow and pressure drop information used to size a valve is based on the process operations and equipment, and ISA Form S20.50 (ISA, 1992) provides a helpful method for recording the data. The size of the valve depends on the pressure drop across the valve. A general guideline for pumped systems is that the valve pressure drop should be 25-33% of the total pressure drop from supply to the end of the pipe (Moore, 1970). To provide appropriate rangeability, the Cv (flow rate) should be determined for the extremes of expected operation. Typically, a valve should be selected that has the maximum Cv value at about 90% of the stem position; this guideline allows for some extra capacity. The valve should have the minimum Cv at no less than 10-15% stem position, which will give a reasonable rangeability, especially since the accuracy of the characteristic is poor below 10% stem position..
For liquids in turbulent flow, the defining equation is the equation for flow through an orifice, which can be rearranged and supplemented with correction factors.

Where
Cv | = | flow coefficient (gallons/min/psi1/2) |
Fliq | = | flow rate (gallons/min) |
FP | = | dimensionless factor accounting for difference in piping due to fittings for piping changes at inlet and outlet; values range from 0.80 to 0.98 and are typically about 0.95 (see Driskell 1983 for details) |
FR | = | dimensionless factor accounting for viscosity effects for liquids; the value is 1.0 for Reynolds numbers greater than 4×104 (see Hutchison 1976 for the calculation of the valve Reynolds number and FR) |
Gliq | = | specific gravity of process fluid at 60 °F (15 °C) |
DP | = | pressure drop across the valve (psi) |
When the process conditions, including the valve (Cv), are known, equation (9) can be used to calculate the flow. When designing the process, the desired flow is known but the valve is not; equation (9) can be rearranged to calculate the valve coefficient required for the specified conditions.
The pressure decreases as the liquid flows through the valve. The possibility exists for the liquid to partially vaporize due the pressure drop, and this vaporization can have serious consequences for the control valve. Two situations can occur: cavitation where the vapor forms and is condensed due to the pressure recovery and flashing where vapor remains after the pressure recovery. The effect of vaporization on the flow is shown in Figure 3. Importantly, cavitation involves the collapsing of bubbles that can generate significant forces that will damage the valve components, so that cavitation should be avoided when designing a flow system. This can be achieved by raising the pressure (e.g., higher supply pressure), lowering the stream temperature (e.g., locating upstream of a heater) or using a valve with little pressure recovery.
Flashing occurs when vapour remains downstream of the valve after the pressure recovery. This situation will not result in damage to the valve and is an acceptable design. Special flow models are required for valve sizing when vaporization occurs and can be found is standard references, e.g., Driskell (1983).
For gases and vapours with subsonic flow, the development of the equation is similar but must consider the change in density with an expansion factor and the lack of ideal behaviour with the compressibility.

Where
Fg | = | gas flow rate (std. ft3/h) |
Gg | = | specific gravity of the process fluid relative to air at standard conditions |
N | = | unit conversion factor (equal to 1380 for English units) |
P1 | = | upstream pressure (psia) |
T1 | = | upstream temperature (°R) |
Y | = | dimensionless expansion factor which depends on P1/P2 and the specific heat ratio; ranges from 0.67 to 1.0 (see Driskell 1983) |
z | = | compressibility factor |
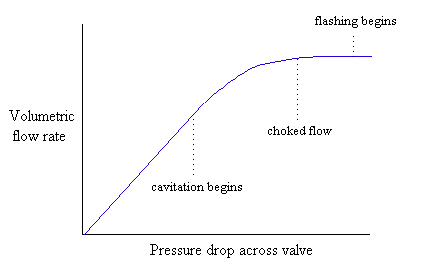
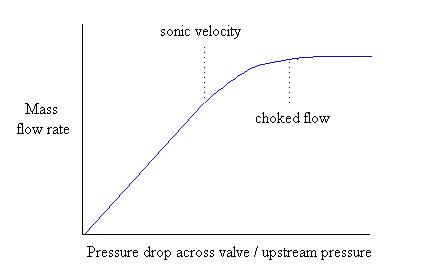
When the pressure drop across the valve is large, sonic flow can occur which will require special calculations for valve sizing (Hutchison, 1976). The general behaviour of flow versus pressure drop is shown in Figure 4. When choked flow occurs, the downstream pressure does not influence the flow rate. A rough guideline is that sonic flow does not occur when the pressure drop is less than 42% of the supply pressure. Sonic flow through valves occurs often and does not represent difficulties when the proper valve trim design and materials are used.
Special models are available for unique situations like sonic flow, mixed phase flow, slurries, excessive vibration and noise, and condensation in the valve. See Hutchison (1976) and Driskell (1983) for details.
Additional Control Valve Equipment |
Additional equipment is required for good control valve performance, and a few of the more important items are described in this section.
Actuator: The actuator provides the power that is used to move the valve stem and plug. The power source used in the process industries for the vast majority of the actuators is air because it is safe and reliable. Many actuators are described as diaphragm because the pneumatic signal pressure is transmitted to the actuator volume that is sealed with a flexible diaphragm. As shown in Figure 16, the valve stem is connected to the diaphragm, as is a spring that forces the valve to be either fully opened or fully closed when the opposing air pressure in the diaphragm is atmospheric. The diaphragm pressure is equal to the pneumatic control signal, usually 3-15 psig representing 0-100% of the signal, which forces the diaphragm to distort and moves the valve stem to the position specified by the control signal.
Booster: The flow rate of air in the pneumatic line is not large and significant time may be required to transfer sufficient air into the actuator so that the actuator pressure equals the line pressure. This time slows the dynamic response of the closed-loop system and can degrade control performance. When the delay is significant in comparison with the other elements in the control loop, a booster can be located in the pneumatic line near the valve which increases the volumetric flow rate of air and greatly speeds the dynamic response of the actuator.
Failure position: Major failures of control equipment, such as the break of a pneumatic line or air compressor, lead to a low (atmospheric) pressure for the signal to the actuator. In such situations, where control has been lost, the valve should be designed to attain the safest possible position, which is usually fully opened or closed. The proper failure position must be determined through a careful analysis of the specific process; usually, the pressure and temperature near atmospheric are the safest. The failure position is achieved by selecting the design in which the actuator valve places the valve stem in its safest position. The design is usually described as fail open or fail closed. Other failure modes can be achieved in response to unusual circumstances, for example, fail to a fixed position and fail slowly to the safe position.
Positioner: The valve is a mechanical device that must overcome friction and inertia to move the stem and plug to the desired position. Typically, the valve does not achieve exactly the position specified by the control signal. This imperfection may not be significant because feedback controllers have an integral mode to reduce offset to zero at steady state. However, the difference might degrade control performance, especially in a slow control loop. A positioner is a simple, proportional-only controller that regulates the measured stem position close to the value specified by the control signal to the valve. For further discussion on positioners, see Hutchison (1976).
Hand wheel: Some control valves must occasionally be set to specified positions by personnel located at the process equipment. A manual hand wheel provides the ability for local personnel to override the control signal to the valve.
Steps in Selecting a Control Valve |
The basic steps in control valve selection are presented below.
- The first step in control valve selection involves collecting all relevant data and completing the ISA Form. The piping size must be set prior to valve sizing, and determining the supply pressure may require specifying a pump. The novice might have to iterate on the needed piping, pump pressure and pressure drop through the piping network.
- Next, the size of the valve is required; select the smallest valve Cv that satisfies the maximum Cv requirement at 90% opening. While performing these calculations, checks should be made regarding flashing, cavitation, sonic flow and Reynolds number to ensure that the proper equation and correction factors are used. As many difficulties occur due to oversized valves as to undersized valves. Adding lots of “safety factors” will result in a valve that is nearly closed during normal operation and has poor rangeability.
- The trim characteristic is selected to provide good performance; goals are usually linear control loop behavior along with acceptable rangeability.
- The valve body can be selected based on the features in Table 2 and the typical availability in Table 3. Note that the valve size is either equal to the pipe size or slightly less, for example, a 3-inch pipe with a 2-inch globe valve body. When the valve size is smaller than the process piping, an inlet reducer and outlet expander are required to make connections to the process piping.
- The actuator is now selected to provide sufficient force to position the stem and plug.
- Finally, auxiliaries can be added to enhance performance. A booster can be increase the volume of the pneumatic signal for long pneumatic lines and large actuators. A positioner can be applied for slow feedback loops with large valves or valves with high actuator force or friction. A hand wheel is needed if manual operation of the valve is expected.
Table 3. Information on Standard Commercial Control Valves1
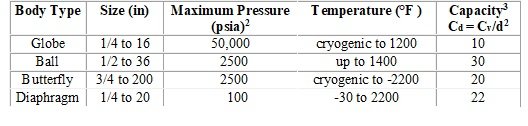
- Compiled from Andrew and Williams (1980) and Driskell (1983)
- Higher pressures for smaller sizes and moderate temperatures.
- The parameter d is the valve connection diameter in inches.
Valve Installation |
Many important factors must be considered when designing the physical installation of the control valve. Perhaps the most important is the design of piping for manual bypass. A control valve may require periodic maintenance to correct leaks, noise, vibration, increasing dead band, and so forth. Since a plant shutdown usually involves a large economic penalty, an incentive exists to maintain plant operation while the control valve is being repaired in many, but not all, situations. The bypass system shown in Figure 5 provides the ability to “block” out the control valve while the process flow passes through the manual bypass valve. The performance is best when the design includes 10-20 diameters of straight run piping in the inlet and 3-5 diameters in the outlet. An operator must close the block valves and manipulate the bypass valve to achieve some desired operating condition, such as flow rate or temperature. For a typical globe valve, the valve should be installed so that the stem moves vertically with the actuator above the valve. In addition, the valve should be located with enough clearance from other equipment so that maintenance can be performed on the valve.
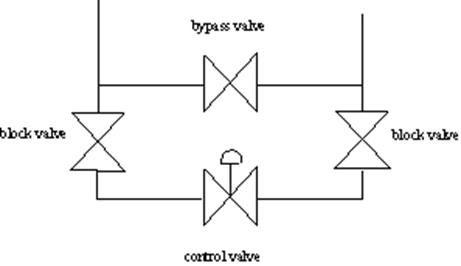
Control valves are used to affect the flow rate in a pipe, i.e., they are used to throttle flow. Control valves do not provide reliable, tight closure, so that some small flow rate can be expected when the valve is “fully closed”. The amount of leakage depends upon the valve body and the fluid.