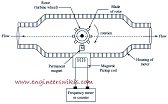
A turbine flow meter is a type of flow meter used to measure the flow rate of liquids and gases. It operates on the principle of a rotating turbine placed in the fluid stream. As the fluid flows through the meter, it impinges on the turbine blades, causing the turbine to rotate. The rate of rotation is directly proportional to the velocity of the fluid, and thus, the flow rate can be determined by measuring the rotational speed of the turbine.
Below are the key features and components of a typical turbine flow meter:
- Turbine Assembly: It consists of a rotor with multiple blades or vanes that rotate when fluid passes through them. The turbine assembly is designed to provide a balanced response to flow, ensuring accurate measurements.
- Housing: The turbine assembly is enclosed within a housing or body, usually made of metal or plastic. The housing includes inlet and outlet ports that allow the fluid to pass through.
- Bearings: The turbine assembly is supported by bearings to minimize friction and allow smooth rotation. Precise bearing design is crucial for maintaining accuracy and reducing wear on the moving parts.
- Sensors: Turbine flow meters often include magnetic or optical sensors positioned near the rotating turbine to detect blade movement. These sensors generate electrical signals, which are then processed to determine the flow rate.
- Signal Processing and Display: The electrical signals from the sensors are processed by electronics within the flow meter. The processed data is typically displayed on a digital or analog display, providing real-time flow rate information.
Following are the advantages of Turbine flow meters :
- Wide range of flow measurement: Turbine flow meters can handle a broad range of flow rates, from low to high velocities, making them suitable for various applications.
- Accuracy: With proper calibration and installation, turbine flow meters can provide accurate flow rate measurements.
- Compact size: Turbine flow meters are relatively compact and can be easily integrated into existing piping systems.
- Versatility: They can be used for measuring the flow of both liquids and gases, making them versatile for different industries and applications.
Following are the limitations of turbine flow meters:
- Sensitivity to fluid properties: Turbine flow meters can be sensitive to changes in fluid properties such as viscosity, density, and temperature. Variations in these properties can affect the accuracy of the flow measurements. It is important to calibrate the flow meter for the specific fluid being measured to minimize errors.
- Limited to clean fluids: Turbine flow meters are typically not suitable for measuring fluids that contain solid particles or debris. Particles in the fluid can interfere with the turbine blades, leading to damage or inaccurate readings. In applications where the fluid contains solid impurities, alternative flow meter technologies like magnetic flow meters or ultrasonic flow meters may be more appropriate.
- Pressure drop: Turbine flow meters create a pressure drop as the fluid passes through the meter. This pressure drop can be significant, particularly in high flow rate applications. It is necessary to consider the pressure drop and ensure that it does not adversely affect the system or the overall process.
- Limited turndown ratio: Turndown ratio refers to the range of flow rates that a flow meter can accurately measure. Turbine flow meters typically have a limited turndown ratio compared to some other flow meter types. In low flow rate conditions, the turbine may not rotate with sufficient speed to provide accurate measurements.
- Mechanical wear and maintenance: Turbine flow meters consist of moving parts, including the turbine blades, which can be subject to mechanical wear over time. The presence of abrasive or corrosive fluids can accelerate this wear, requiring regular maintenance or replacement of parts to maintain accuracy. Additionally, the meter may require periodic calibration to ensure precise measurements.
- Flow profile sensitivity: Turbine flow meters require a well-developed flow profile to achieve accurate readings. Irregular flow profiles, such as those with turbulence or swirl, can result in distorted measurements. Therefore, it is often recommended to install straight pipe runs or flow conditioners upstream of the meter to ensure a stable flow profile.