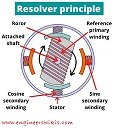
A resolver is an electrical device that converts mechanical motion into electrical signals, or vice versa. It is commonly used in applications where precise control of motion is required, such as in robotics, CNC machines, and other mechatronic systems.
The resolver consists of a rotor and a stator, which are arranged in a cylindrical shape. The rotor is attached to a shaft, which is connected to a motor or other mechanical device. The stator has a series of windings that are connected to a controller or other electronic device.
When the shaft rotates, the rotor moves within the stator, causing the windings to generate electrical signals that represent the position and velocity of the shaft. These signals are then processed by the controller to determine the precise position and velocity of the shaft, and to control the motion of the motor or other mechanical device.
Resolvers are typically used in applications where high precision and accuracy are required, such as in robotic arms, CNC machines, and other mechatronic systems. They offer several advantages over other position sensing technologies, including high resolution, high accuracy, and resistance to noise and interference.
There are several types of resolvers available, including incremental resolvers, absolute resolvers, and hybrid resolvers. Incremental resolvers provide a continuous signal that indicates the position of the shaft, while absolute resolvers provide a unique signal for each position of the shaft. Hybrid resolvers combine the features of incremental and absolute resolvers, offering both precise positioning and continuous monitoring of the shaft’s position.
In summary, resolvers are an essential component in many modern technologies, providing precise control of motion and positioning in a wide range of applications. They offer several advantages over other position sensing technologies, including high resolution, high accuracy, and resistance to noise and interference.
What are applications where hybrid resolvers are used?
Hybrid resolvers are used in a variety of applications that require both precise positioning and continuous monitoring of a shaft’s position. Some common applications include:
- Robotics: Hybrid resolvers are used in robotic arms and grippers to provide precise positioning and control of the robot’s movements.
- CNC Machines: Hybrid resolvers are used in computer numerical control (CNC) machines, such as lathes, milling machines, and grinders, to provide precise positioning and control of the cutting tool.
- Machine Tools: Hybrid resolvers are used in machine tools, such as drill presses and saws, to provide precise positioning and control of the tool.
- Automotive: Hybrid resolvers are used in various automotive applications, such as in engine management systems, transmission control systems, and brake systems.
- Aerospace: Hybrid resolvers are used in aerospace applications, such as in navigation systems, control systems, and engine management systems.
- Medical Equipment: Hybrid resolvers are used in medical equipment, such as in surgical robots, imaging machines, and radiation therapy machines, to provide precise positioning and control of the equipment.
- Industrial Automation: Hybrid resolvers are used in industrial automation applications, such as in conveyor systems, cranes, and hoists, to provide precise positioning and control of the equipment.
- Power Tools: Hybrid resolvers are used in power tools, such as in drills, saws, and grinders, to provide precise positioning and control of the tool.
- Textile Machinery: Hybrid resolvers are used in textile machinery, such as in looms, knitting machines, and embroidery machines, to provide precise positioning and control of the machine’s movements.
- Food Processing: Hybrid resolvers are used in food processing machinery, such as in packaging machines, cutting machines, and sorting machines, to provide precise positioning and control of the machine’s movements.