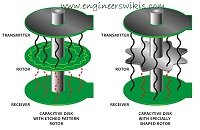
Capacitive Encoders
Capacitive encoders are a type of contactless measurement device used in a variety of applications where precise position or displacement measurement is needed. They work on the principle of detecting changes in electrical capacitance to infer changes in position.
Working Principle
The fundamental principle behind a capacitive encoder is the measurement of the electrical capacitance between two plates. Capacitance is a measure of an object’s ability to store electrical charge. It is directly proportional to the area of the plates and inversely proportional to the distance between them. In a capacitive encoder, one of these parameters (usually the distance) is variable and changes in response to the movement of the target object.
The encoder consists of a stationary sensor (or stator) and a moving target (or rotor). As the rotor moves, the distance between the stator and rotor changes, leading to variation in the capacitance. This change in capacitance is detected and converted into an electrical signal which can then be interpreted as a change in position.
Types of Capacitive Encoders
There are two primary types of capacitive encoders:
- Linear Capacitive Encoder: This type of encoder measures change in position along a linear path. The encoder consists of two parallel plates, one fixed (stator) and the other movable (rotor). As the movable plate changes its position, the capacitance between the two plates changes, which is then converted into a linear displacement.
- Rotary Capacitive Encoder: This type of encoder measures the change in angular position. The encoder consists of two concentric circular plates, one fixed (stator) and the other movable (rotor). As the rotor rotates, the capacitance between the two plates changes, which is then converted into an angular displacement.
Applications
Capacitive encoders are used in a wide range of applications, including:
- Precision positioning in micro-manufacturing processes
- Robotics for precise control of robot arms
- Medical devices such as MRI machines for precise positioning of components
- Aerospace industry for control systems
- Consumer electronics such as touch-sensitive devices (touch screens, touchpads, etc.)
Advantages and Disadvantages
Advantages:
- High resolution and accuracy
- Contactless operation reduces wear and tear
- Not affected by external magnetic fields
- Can be used in a wide range of environmental conditions
Disadvantages:
- Sensitive to changes in temperature and humidity
- More expensive compared to other types of encoders
- Requires sophisticated electronics for signal processing