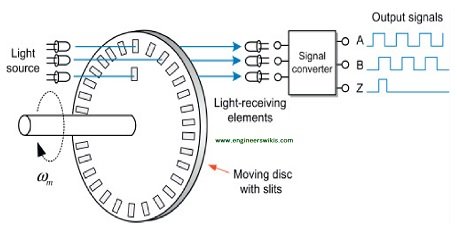
An incremental optical encoder is a type of encoder that uses optical technology to measure and provide position feedback. It is widely used in various applications where precise position and speed control are required. Here’s how an incremental optical encoder typically works:
Working Principle:
An incremental optical encoder consists of a rotating disc or code wheel with evenly spaced transparent and opaque sections, and a stationary optical sensor assembly. The disc is mounted on the motor shaft or the rotating object whose position needs to be monitored. As the disc rotates, the optical sensor detects the transitions between the transparent and opaque sections, generating electrical signals that indicate the movement and position changes.
Encoder Output:
The output of an incremental optical encoder consists of two or more channels, usually labeled as A, B, and sometimes Z. The A and B channels provide quadrature output, which means they produce pulse trains with a phase difference of 90 degrees. The phase relationship between the A and B channels indicates the direction of rotation. The Z channel, if present, is known as the index channel and provides a single pulse per revolution, allowing for absolute referencing or position initialization.
Encoder Signals:
The A and B channels of an incremental optical encoder generate square wave signals. When the disc rotates, the A and B channels produce pulses that correspond to the transitions between transparent and opaque sections. By counting these pulses and monitoring the phase relationship, the position, speed, and direction of rotation can be determined.
Resolution:
The resolution of an incremental optical encoder is determined by the number of transparent and opaque sections on the disc. It is usually specified as pulses per revolution (PPR) or counts per revolution (CPR). Higher resolution encoders have more sections on the disc, allowing for finer position control and measurement.
Applications:
Incremental optical encoders find applications in various industries and systems, including:
- Robotics and Automation: They are used in robotic arms, CNC machines, and automated systems for precise position control and feedback.
- Motion Control Systems: Incremental optical encoders are widely used in servo motors and stepper motors to provide accurate position feedback for closed-loop control.
- Industrial Machinery: They are employed in machine tools, printing presses, conveyor systems, and other industrial machinery for speed and position control.
- Packaging and Labeling Equipment: Incremental optical encoders are used in packaging and labeling machines to ensure accurate positioning and synchronization.
- Consumer Electronics: They can be found in audio equipment, cameras, printers, and various consumer electronics for functions like volume control, menu navigation, and motion detection.
Incremental optical encoders offer advantages such as high resolution, compact size, and reliability. However, it’s important to note that they provide relative position information and require a reference point (index pulse) for initialization. To obtain absolute position feedback, additional circuitry or a combination with other types of encoders may be necessary.
There are some limitations and drawbacks associated with using incremental optical encoders. Here are a few to consider:
- Lack of Absolute Positioning: Incremental optical encoders provide relative position information based on pulse counts. They do not inherently provide absolute position feedback without additional circuitry or a reference point. If power is lost or the system is restarted, the encoder’s position needs to be reinitialized. This limitation can be overcome by using additional encoders or sensors for absolute positioning or by incorporating a reference point (index pulse) in the encoder design.
- Susceptibility to Signal Interference: Optical encoders, including incremental optical encoders, rely on light transmission and detection. They can be susceptible to external factors such as ambient light, dust, and contaminants, which can interfere with the optical sensor’s ability to accurately detect the transitions on the code wheel. Adequate shielding and proper installation can help mitigate this issue.
- Limited Environmental Robustness: Optical encoders, including incremental optical encoders, may be more sensitive to harsh environmental conditions compared to other types of encoders. Factors such as moisture, temperature extremes, vibrations, and shocks can affect the performance and reliability of the optical components. In applications with demanding environmental conditions, alternative encoder types like magnetic or inductive encoders may be more suitable.
- Lower Accuracy at Low Speeds: Incremental optical encoders may exhibit reduced accuracy at low speeds or during motor startup and shutdown. This limitation is due to the fact that the encoder relies on detecting changes in the optical pattern on the disc, and at very low speeds, the pulses may not be consistently detected. If high accuracy is required at low speeds, alternative encoder types or additional sensors may be necessary.
- Limited Resolution: While incremental optical encoders can provide high resolution, their resolution is ultimately constrained by the number of transparent and opaque sections on the disc. Achieving extremely high resolutions may require larger and more intricate code wheels, which can increase costs and physical space requirements.
- Cost Considerations: Incremental optical encoders can be cost-effective for many applications, but their cost can increase with higher resolutions and additional features like index channels. If the application requires very high resolutions or absolute position feedback, alternative encoder types may offer more cost-effective solutions.