Hydraulics
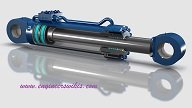
The basic principle of hydraulics relies on Pascal’s law, which states that when pressure applied to a confined fluid, the pressure transmitted equally in all directions. This principle allows hydraulic systems to multiply force or torque, making them suitable for a wide range of applications.
Hydraulic systems widely used in various industries and applications. Some common examples include heavy machinery and construction equipment (such as cranes, excavators, and forklifts), hydraulic presses, braking systems in vehicles, aircraft flight controls, hydraulic lifts, and power steering systems.
The advantages of hydraulic systems include high power density, precise control, and the ability to transmit power over long distances. However, they also have some limitations, such as the need for regular maintenance, potential leakage issues, and the requirement for a power source (usually an electric motor or an engine) to drive the hydraulic pump.
Applications of hydraulic systems
- Construction machinery: Hydraulic systems extensively used in construction equipment like excavators, bulldozers, cranes, loaders, and backhoes. They enable precise control of heavy machinery, lifting and moving of loads, and provide stability and safety.
- Aerospace industry: Hydraulic systems are crucial in aircraft for operating landing gear, brakes, flight control surfaces, and other critical functions. They provide reliable and precise control in extreme conditions.
- Automotive industry: Hydraulic systems used in vehicles for power steering, braking systems, suspension systems, and automatic transmissions. They help enhance vehicle performance, safety, and comfort.
- Manufacturing machinery: Hydraulic systems utilized in various manufacturing processes, such as metal stamping, injection molding, hydraulic presses, and machine tools. They provide high force and precision control for shaping, cutting, and forming materials.
- Agricultural machinery: Hydraulic systems employed in agricultural equipment like tractors, combines, and harvesters. They enable lifting and lowering of implements, power transmission, steering, and control of attachments.
- Material handling equipment: Hydraulic systems used in forklifts, cranes, and conveyor systems for lifting, moving, and manipulating heavy loads. They offer strength, stability, and precise control for efficient material handling.
- Marine industry: Hydraulic systems are vital for ships and offshore structures. Hydraulic systems used in steering systems, winches, cranes, and cargo handling equipment. Hydraulic systems provide reliable control in harsh marine environments.
- Power generation: Hydraulic systems utilized in hydroelectric power plants for turbine control, gate operation, and dam safety systems. They enable efficient conversion of water flow into electrical energy.
- Robotics: Hydraulic systems employed in certain types of robots for lifting heavy objects, providing force feedback, and executing precise movements. They often used in industrial automation and manufacturing processes.
Advantages of using hydraulic systems in the manufacturing industry:
- High force and power transmission: Hydraulic systems can generate significant force and power, allowing them to handle heavy loads and perform demanding tasks in manufacturing processes. They provide the necessary strength for operations such as metal stamping, pressing, and lifting.
- Precise control: Hydraulic systems offer precise control over movements and forces, enabling accurate positioning and manipulation of machinery and tools. This level of control is crucial in applications like machining, welding, and assembly, where precision is essential.
- Safety and overload protection: Hydraulic systems can incorporate safety features such as pressure relief valves and overload protection mechanisms. These features prevent damage to equipment and ensure the safety of operators by regulating pressure and preventing excessive force.
- Versatility: Hydraulic systems can be adapted to various manufacturing applications and integrated into different types of machinery. They can be customized to meet specific requirements, making them versatile and suitable for a wide range of manufacturing processes.
- Energy efficiency: Hydraulic systems designed to be energy-efficient by using variable displacement pumps, accumulators, and energy recovery systems. They can minimize energy consumption by delivering power only when needed and storing excess energy for later use.
- Durability and reliability: Hydraulic systems are known for their durability and reliability. They can withstand harsh operating conditions, such as high temperatures, vibrations, and contaminants, making them suitable for demanding manufacturing environments.
- Compact design: Hydraulic systems can be designed with a compact form factor, allowing them to be integrated into machinery with limited space. This is particularly advantageous in manufacturing plants where space optimization is important.
- Smooth and controlled operation: Hydraulic systems provide smooth and controlled operation due to the incompressibility of hydraulic fluids. This enables precise movements, reducing the risk of jerky motions that could affect product quality or damage machinery.